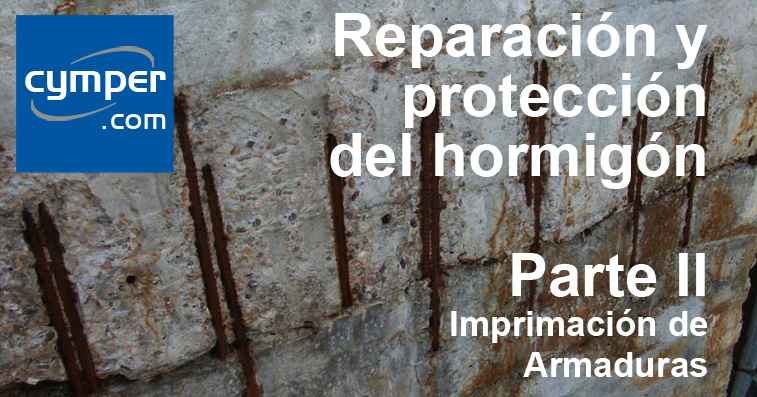
Al reparar hormigón armado generalmente se observa que la armadura está oxidada. La protección natural del acero, consistente en una capa pasivadora a su alrededor formada por la condición alcalina del cemento, se pierde debido principalmente al ataque de cloruros o a la carbonatación.
La carbonatación provoca la oxidación a lo largo de toda la armadura, debido a que en el entorno de la armadura se ha perdido la alcalinidad. En ausencia de otros factores tales como cloruros, los efectos de la carbonatación se apreciarán a medio o largo plazo.
A diferencia de la carbonatación, la oxidación por ataque de cloruros está localizada en zonas concretas. Dicha oxidación resulta más severa y destructiva que la provocada por la carbonatación produciendo una pérdida de la sección de la armadura que puede ocasionar fallos de gran alcance en las estructuras de hormigón.
La pérdida de sección o la formación de hendiduras debido al ataque de iones cloruro es debido a que estos últimos descomponen la barrera pasivadora formada por óxido de hierro que rodea la superficie del acero. Esto permite que el hierro pase a disolución en forma de iones ferrosos (Fe 2+), lo cual provoca la formación de un ánodo. Este ánodo atraerá hacia sí más iones cloruro cargados negativamente (CI-), y como consecuencia, más hierro pasa a la disolución lo cual conlleva una pérdida de sección o formación de hendiduras cada vez más profundas. Esta reacción libera electrones que migran a través de la armadura a otra zona donde reaccionan con el oxígeno y agua para formar iones hidróxilo (OH-). Como consecuencia esta zona se convierte en un cátodo, sentando así las bases de una reacción electroquímica.
Es importante apuntar que en el cátodo no se produce corrosión y de hecho esta zona de la armadura está protegida al no atraer hacia sí iones cloruro.
Los iones hidróxilo producidos en el cátodo se difunden a través de la disolución acuosa existente en los poros del hormigón hasta que reaccionan con los iones ferrosos provenientes del ánodo. El producto de esta reacción es el hidróxido de hierro que con el tiempo se convierte en óxido. Estas reacciones se ilustran en la figura 1.
Figura 1. Mecanismo de reacción de oxidación por iones cloruros
Reacción en el ánodo:
Reacción en el cátodo:
Reacción global:
Es importante tener en cuenta que el objeto de cualquier reparación es evitar la formación de ánodos en la superficie de la armadura, tanto en las zonas reparadas, como en el hormigón adyacente. Así evitamos que el hierro se oxide y pase a la disolución.
Antes de llevar a cabo una reparación es importante investigar las causas y la magnitud del deterioro. Esto puede incluir, por ejemplo, la prueba de la fenolftaleína para detectar la carbonatación, medición de los potenciales de corrosión y análisis de cloruros para localizar las posibles zonas de corrosión.
El hormigón deteriorado se debe eliminar completamente. Las armaduras que presenten corrosión deberán descubrirse en todo su perímetro y longitudinalmente hasta la aparición de aproximadamente 50 mm de armadura sana a cada extremo de la zona corroída. A continuación tanto la armadura como el substrato se deben chorrear con arena para eliminar todo el óxido o cualquier otra sustancia contaminante y además para obtener una buena base para la reparación.
En este documento vamos a repasar los requisitos, métodos de valoración y resultados de los materiales usados en la reparación y protección de hormigón armado. Esto incluye la imprimación de las armaduras, la imprimación del substrato y el mortero de reparación (Ref 1 ).
Imprimación para las armaduras
Requisitos: Una imprimación para la armadura debe proteger el acero, formar una película continua y penetrante para evitar la oxidación subyacente, tener buena adherencia al acero y al mortero de reparación, no perjudicar a las zonas adyacentes a la aplicación y que sea fácil de utilizar. La armadura se debe limpiar mediante un chorro de arena hasta conseguir una superficie brillante tipo SA 2, 1/ 2 según la norma sueca (Ref 2).
Existen muchas técnicas y tipos de imprimación para armaduras como por ejemplo:
- Sin imprimación
- Lechada cementosa
- Lechada cementosa modificada con polímeros
- Resina epoxi sin pasivador
- Resina epoxi con pasivador
- Resina epoxi-zinc (de uno o dos componentes)
Valoración: Para determinar la eficacia de estos sistemas se utilizan métodos de ensayos de envejecimiento acelerado. Uno de ellos se basa en observar el comportamiento de probetas reparadas con cada uno de los sistemas, después de ser sometidas a 52 ciclos consistentes en 5 días en una cámara de niebla salina a 40 °C, 1 día de hielo/deshielo y 1 día a 20 °C y 65% de humedad relativa (Ref 3). Mediante otros ensayos se ha medido la resistencia al deslizamiento de barras imprimadas, sometidas a esfuerzos axiales y también la resistencia a cortadura entre el mortero de reparación y el substrato cuando éste ha sido previamente contaminado con la imprimación (Ref 4).
Resultados y Discusión: Se encontró que las armaduras sin imprimación o imprimadas con una lechada de cemento, ofrecían excelente protección al acero en la zona reparada. Sin embargo la oxidación del acero en las áreas adyacentes a la zona reparada fue acelerada.
Se cree que este efecto es debido a que la alta alcalinidad de la lechada cementosa crea una zona catódica en la zona reparada y, como consecuencia, se forma un posible ánodo en la armadura del hormigón adyacente capaz de atraer iones cloruros y corroerse.
También se observó que las imprimaciones a base de lechadas de cemento modificadas con polímeros, resinas epoxi sin pasivador y resinas epoxi con cargas pasivadoras como por ejemplo fosfato de zinc y clinker de cemento, no formaban una película continua y penetrante produciéndose una oxidación subyacente. La razón por la cual se produce esta oxidación subyacente es que dichos sistemas probablemente aíslan a la armadura de la alta alcalinidad del mortero de reparación y por lo tanto evitan la pasivación de la armadura. Cuando se utilizaron cargas pasivadoras, se apreció que éstas estaban totalmente ligadas a la película que formaba el polímero/epoxi y por lo tanto ofrecían poca actividad. Investigaciones recientes han sugerido que cementos modificados con polímeros conteniendo inhibidores de óxido, micro sílice y arena pueden dar buenos resultados ya que no se produce la oxidación subyacente. Sin embargo su efecto sobre la armadura en el hormigón adyacente es aún una incógnita.
En estos ensayos se comprobó que la imprimación rica en zinc, Nitoprime Zincrich, ofrecía una excelente protección a la armadura tanto en la zona reparada como en el hormigón adyacente. Con este sistema el revestimiento de zinc permite un contacto eléctrico entre la armadura y el zinc activo. De esta forma el zinc hace las funciones de ánodo y protege así la armadura en la zona reparada mientras que la armadura en el hormigón adyacente hace de cátodo. No se apreció ningún ataque químico del mortero de reparación cementoso sobre la imprimación de zinc.
Para comprobar el efecto de la imprimación sobre la adherencia, se llevaron a cabo ensayos de tracción. Dichos ensayos demostraron que la imprimación de epoxi/zinc no tenía efectos significativos sobre la adherencia entre el mortero y armadura (chorreado con arena según SA 2-1/2) Los resultados de dichos ensayos se reflejan en la Tabla 1.
Tabla 1: Efecto sobre la adherencia de armaduras imprimadas (chorreadas con arena según SA 2-1/ 2)
ancladas en un agujero de 32 mm de diámetro en un hormigón de 600 Kg/cm2, utilizando para su anclaje
una lechada cementosa de una resistencia a compresión de 650 Kg/cm2.
También se han llevado a cabo ensayos de adherencia en plano inclinado según BS 6319 para comprobar la adherencia entre el substrato y el mortero de reparación ante el supuesto de que la imprimación Nitoprime Zincrich pudiera contaminar accidentalmente la superficie del hormigón. Los resultados indicaron que el efecto sobre la adherencia era
insignificante.
Conclusiones: Estos ensayos han demostrado que la imprimación monocomponente epoxi/zinc ofrece la mejor protección contra la corrosión de las armaduras, tanto en la zona reparada como en el hormigón adyacente. El sistema monocomponente es más fácil de usar y más económico que el de 2 componentes. Además se consigue una excelente adherencia.
¿Te ha resultado útil esta información?. Si te ha gustado lo que has leído, nos encantaría que lo compartas con tus redes y que te unas a nuestra comunidad.
También puede ver toda la variedad de productos relacionados en:
- Reparación y protección del hormigón ( Parte I ) – Introducción
- Reparación y protección del hormigón ( Parte II ) – Imprimación de Armaduras
- Reparación y protección del hormigón ( Parte III ) – Imprimación del substrato de hormigón
- Reparación y protección del hormigón ( Parte IV ) – Morteros de reparación
- Reparación y protección del hormigón ( Parte V ) – Microhormigón
- Reparación y protección del hormigón ( Parte VI ) – Casos especiales
Referencias:1.- Informen.º 26 del Concrete Society Technical «Repair of concrete damaged by reinforcement corrosion». The Concrete Society, Londres.2.- Norma sueca SIS 05 5900.3.- McCurrich, Keeley, Cheriton, Turner: «Mortar Repair Systems-Corrosion Protection for Damaged Reinforced Concrete». Actas del congreso SCI «Corrosion of reinforcement in concrete construction», Londres, junio 1983 Editor A P Grane Ellis Horwood Chichester.4.- BS 6319, part. 4. British Standards 1984.5.- Tabor. «Twist old and New: Achieving a Bond when Casting Fresh Concrete against Hardened Concrete». Actas de la 2.ª Conferencia Internacional sobre Fallos Estructurales y Reparación, del 30/ de al 2/5 de 1985. Engineering Technics Press Edinburgo.6.- Dennis: «Latex in the Construction lndustry» publicado en «Chemistry & lndustry» n.º 15 de la página 505 a 511 de agosto de 1985.7-. Treadway y Russell, Building Research Station, página 82 de 1988.8.- Pourbaix, «Lectures in Electrochemical Corrosion» Capítulo 6, Premium Press 1973.9.- Pfeifer y Scall, «Concrete Sealers for Protection of Bridge Structures», del informe 244 del National Cooperative Highway Research Programe. Transport Research Board, Washington DC USA, Diciembre, 1981.10.- McCurrich, Whitaker, Humpage, «Reduction in rates of Carbonatation and Chloride lngress by Surface lmpregnation». Actas de la 2.ª conferencia internacional sobre Fallos Estructurales y Reparación, 30/4 al 2/5, de 1985. Engineering Technics Press, Edimburgo.